O Lean Manufacturing (em português, Manufatura Enxuta) foi desenvolvido na Toyota como parte do Sistema de Produção Toyota, que foi construído em torno do trabalho de Walter Shewhart e Edward Deming, sendo que a Toyota era cliente de Deming e estabeleceu as suas práticas de gerenciamento operacional com base nos princípios em que ele ensinava.
Onde foram formados os princípios de Lean e por que é bom unir o Lean ao Six Sigma?
Os princípios de Lean Manufacturing surgiram no Japão nos anos 40. Em um esforço para melhorar as vendas e aumentar o lucro da Toyota, Eiji Toyoda embarcou em uma jornada para melhorar os processos de fabricação da Toyota.
![]() |
Foto de Eiji Toyoda (a esquerda) e Taiichi Ohno (a direita) |
Em sua visita às instalações da Ford em Michigan, nos Estados Unidos, ele ficou admirado com o processo da empresa que o inspirou a colaborar junto com Taiichi Ohno, para desenvolver uma série de ferramentas nomeada Lean Manufacturing. Décadas após isso, a sua metodologia irmã Six Sigma surgiu na Motorola nos anos 80.
Ai você me pergunta por que é interessante usar as duas metodologias combinadas?
Embora elas possam ser ensinadas como métodos separados, o ensino em si fica melhor quando se aplica os conhecimentos das duas combinadas, pois assim dá para se colher o melhor dos dois mundos, e por isso eu recomendo que você aproveite depois para ler a nossa postagem sobre Six Sigma, para assim poder ver as similaridades e as diferenças dessas metodologias irmãs.
Lembrando que a compreensão das duas metodologias e o uso das ferramentas delas são extremamente valiosos na solução de problemas.
Entendendo o que é Lean Manufacturing
O fator fundamental do Lean Manufacturing é a eliminação de desperdícios. De fato, uma boa descrição da abordagem Lean é "um conjunto de ferramentas que auxiliam na identificação e na eliminação constante de resíduos".
Se uma empresa produz em grande escala e em grande quantidade como a Toyota, então, um processo com desperdício significa que a empresa está criando resíduos em grande escala e em grande quantidade. Nenhuma empresa quer fazer isso. A abordagem Lean usa ferramentas para analisar o processo de negócios.
Cinco princípios do Lean Manufacturing
Os cinco princípios do Lean Manufacturing são a base do sucesso da Toyota e podem ajudar as empresas a criar produtos centrados no que os clientes desejam, sendo que além disso, também nos ajuda a entender e a otimizar os processos.
![]() |
Cinco princípios do Lean Manufacturing |
Esses princípios são divididos em:
1 – Especificação do Valor
O primeiro princípio do Lean é a especificação do valor, que também é o primeiro passo na jornada para se tornar Lean. Esta etapa requer que as empresas definam o que os clientes valorizam e consideram importante dentro de um produto ou serviço, e não pelo que as pessoas que desenvolvem ou entregam o produto ou serviço consideram importante.
Logo, o valor requer:
- Design de produtos para atender às necessidades dos clientes;
- Remoção de recursos que não atendem especificamente a essas necessidades, que você vai ver mais a frente que isso é um desperdício.
Ao projetar produtos para atender as necessidades específicas dos clientes, as empresas devem eliminar etapas desnecessárias que podem ser necessárias para recursos indesejados.
O Design for Six Sigma (DFSS) é um método bem interessante que pode ajudar as empresas a identificar valor, sendo que usando esse método, as empresas podem definir sistematicamente, medir e analisar o que os seus clientes desejam da maneira correta. Logo, as empresas podem então projetar produtos personalizados para seus clientes.
2 – Mapeamento do Fluxo de Valor
O segundo princípio do Lean Manufacturing é o mapeamento do fluxo de valor. Um fluxo de valor é o ciclo de vida completo de um produto, que vai desde do conjunto de atividades de negócios e etapas envolvidas na criação do design e entrega dos produtos e serviços ao cliente, o uso, ao descarte destes; sendo isso a conexão de todas as etapas juntas, em vez de se considerar cada etapa isoladamente.
Esta etapa requer que as empresas identifiquem e mapeiem o fluxo de valor do produto. Uma ferramenta de Lean Manufacturing muito boa para isso é o VSM ("Value Stream Mapping") que pode ser usado para mapear visualmente todo o fluxo do produto. Depois que o fluxo de valor for mapeado, será mais fácil encontrar e minimizar as etapas que não agregam valor.
3 – Fluxo Continuo
O terceiro princípio Lean é criar um fluxo contínuo e ininterrupto de atividades que agrega valor ao cliente. O fluxo contínuo eficiente de produtos requer que os itens passem da produção para a remessa sem interrupção e podem ser alcançados através da organização estratégica da área de trabalho.
Todos os fatores, de pessoas e equipamentos a materiais e remessas, devem ser levados em consideração para garantir que os produtos se movam sem interrupções no processo de produção.
Um piso de trabalho bem organizado resultará em menor tempo de produção, tamanho do estoque e manuseio de material.
4 - Produção puxada
O quarto princípio Lean é o da produção puxada que é basicamente o grau em que o fluxo de valor está processando apenas produtos e serviços para os quais há uma demanda do cliente, em vez de criar algo e esperar que alguém o queira.
O sistema de produção puxada está intimamente relacionado à criação de fluxo, o quarto princípio Lean exige que as empresas usem um sistema de produção baseado em pull (em português, significa puxar).
Já os sistemas de produção tradicionais usam um sistema push (em português, significa empurrar), que começa com a compra de suprimentos e prossegue empurrando o material pelo processo de fabricação, mesmo quando não há um pedido.
Embora os sistemas push sejam fáceis de criar, eles geralmente resultam em grandes estoques e em uma quantidade significativa de trabalho em andamento (Work In Process, WIP), sendo que isso geralmente não é um bom negocio para as empresas, pois um grande estoque é dinheiro parado que gera custos adicionais à empresa.
Para evitar o custo extra, é sempre bom ter um sistema de extração para extrair o pedido de um cliente do departamento de expedição, que solicita novos itens a serem fabricados e sinaliza que é necessário adquirir suprimentos adicionais.
Usando ferramentas de Lean Manufacturing e trabalhando nos princípios Just in Time (JIT) com Heijunka, Kanban e outras técnicas, consegue-se fazer um bom controle do processo reduzindo as falhas no fluxo de produção, pois essas técnicas ajudam as empresas a estabelecer um sistema de tração para controlar o fluxo de materiais em um sistema de produção.
Usando um bom sistema de produção puxada, as empresas tem como beneficio:
- Aumento da produção;
- Maximização do espaço de trabalho utilizável;
- Redução de estoques;
- Eliminação da superprodução e subprodução;
- Eliminação dos erros causados por excesso de WIP.
5 - Procurar pela Perfeição
O princípio final do Lean Manufacturing é a avaliação contínua do desempenho do fluxo de valor para identificar e melhorar o valor criado e entregue ao cliente, em vez de resistir a mudanças que melhoram o processo de criação e entrega de valor ao cliente.
Esse princípio consiste basicamente na busca pela perfeição, sendo este principio um dos mais difíceis de aplicar com sucesso no local de trabalho. A busca pela perfeição exige que as empresas melhorem continuamente suas práticas e geralmente exige uma mudança na cultura do local de trabalho, sendo que isso geralmente não é uma tarefa fácil.
Uma boa sugestão seria o uso do Kaizen que é uma filosofia de melhoria contínua, que pode ajudar as empresas com essas mudanças, criando uma cultura na qual os trabalhadores buscam a perfeição.
O Kaizen se concentra em fazer mudanças pequenas incrementais que exigem que todos os funcionários, sejam eles do escritório ou do chão de fábrica, ajudem a melhorar as práticas de negócios.
Com o tempo, a filosofia Kaizen quase sempre resulta em maior eficiência, custos reduzidos, maior produtividade e produtos de melhor qualidade.
Ferramentas do Lean Manufacturing – 5S e PDCA
O Lean Manufacturing usa diversas ferramentas para otimização de processo, sendo que algumas delas eu já citei acima, e agora eu vou falar de mais duas ferramentas que são bem interessantes para alcançar uma melhoria contínua, sendo elas: 5S e PDCA .
5S (Seiri, Seiton, Seiso, Seiketsu, Shitsuke)
A metodologia 5S é uma metodologia simples que tem um nome oriundo de iniciais de cinco palavras de origem japonesa: Seiri, Seiton, Seiso, Seiketsu, Shitsuke.
O 5S é uma metodologia que foca basicamente em melhorar o local de trabalho removendo itens que não são mais necessários (senso de utilidade), organizar os itens para melhorar a eficiência e o fluxo (senso de ordem), limpar a área para identificar mais facilmente os problemas (senso de zelo), implementar cores de codificação e etiquetas para permanecer consistente com outras áreas (senso de higiene) e desenvolver comportamentos que mantêm o local de trabalho organizado a longo prazo (senso de disciplina).
PDCA (Plan, Do, Check, Action)
O PDCA (também chamado de PDSA, "Deming Wheel" ou "Deming Cycle") foi desenvolvido pelo renomado estatístico Dr. William Edwards Deming nos anos 50, sendo que o próprio Deming chamava o PDCA de "Ciclo de Shewhart", pois seu modelo era baseado em uma ideia de seu mentor, Walter Shewhart.
O PDCA é um ciclo que é divido em quatro estágios simples: Plan, Do, Check, e Action, que em português significa: Planejar, Fazer, Checar, e Agir.
1. Plan - Planejar
A primeira etapa de planejamento é para mapear o que você fará para tentar resolver um problema ou alterar um processo.
Durante esta etapa, você identificará e analisará o problema ou alguma oportunidade de mudança, para desenvolver hipóteses sobre quais são os problemas ou as causas subjacentes por atrás do problema; após isso você decidira qual hipótese irá testar primeiro.
Nos planejamentos considere sempre as seguintes questões:
Qual é o principal problema que precisamos resolver?
Esse é o problema certo que devemos resolver?
Que informações precisamos para entender completamente o problema e a sua causa raiz?
É possível resolvê-lo?
Quais são os recursos que necessitamos para resolver?
Quais são os recursos que nós temos?
Quais são as soluções viáveis para resolver?
Como podemos medir o sucesso dessa solução?
Como os resultados de um teste em pequena escala se traduzem em uma implementação em larga escala?
Durante essa etapa, você pode montar um Diagrama de Afinidade para ajudar você e seus colegas a organizarem um grande número de ideias que vocês podem conseguir no Gemba.
![]() |
Exemplo de Diagrama de Afinidade – o Diagrama de Afinidade é uma ferramenta de brainstorming que visa organizar dados, ideias e descobertas em grupos usando notas autoadesivas (post-it). |
Após determinar o curso de seu plano de ação, anote bem os resultados esperados e lembre-se que você verificará seus resultados com base em suas hipóteses e expectativas na etapa "Checar".
2. Do – Fazer
Nesse segundo é a hora de testar a sua hipótese, ou seja, a sua solução proposta para a resolução do problema. O ciclo PDCA se concentra em mudanças menores e incrementais que auxiliam a otimização dos processos com o mínimo de interrupção.
O teste de sua hipótese deverá ser feito com um projeto de pequena escala, de preferência em um ambiente controlado, para poder avaliar os resultados sem interromper o restante de sua operação. Você pode testar a solução em uma equipe ou dentro de um determinado grupo demográfico.
3. Check - Checar
Após ter concluído a avaliação do teste, é hora de revisar e analisar os resultados. Essa etapa é muito importante, pois ela nos permite avaliar a solução e revisar os planos conforme necessário.
Nessa hora nos vemos: “Será que o plano realmente funcionou?” “Em caso afirmativo, houve algum problema no processo?” “Quais etapas podem ser aprimoradas ou precisam ser eliminadas de futuras iterações?”
Uma avaliação bem feita nessa etapa guiará as suas decisões na próxima etapa; portanto, é importante considerar seus resultados com bastante cuidado.
4. Act - Agir
Nessa última etapa finalmente é hora de agir. Se tudo deu certo conforme o planejado, agora você pode implementar o plano que você havia testado em pequena escala. Esse novo processo agora se torna sua linha de base para futuras iterações do PDCA.
Nessa hora, você deve considerar as seguintes perguntas antes de agir:
- Quais recursos você precisa para implementar a solução em grande escala?
- Que treinamentos serão necessários para uma implementação e adoção bem-sucedidas?
- Como você pode medir e acompanhar o desempenho da solução?
- Quais são as oportunidades de melhoria?
- O que aprendemos que pode ser aplicado em outros projetos?
Além disso, se o plano não deu certo conforme o esperado, você ainda pode voltar à etapa do planejamento para fazer ajustes, e se preparar para uma nova avaliação.
Tipos de desperdícios a serem evitados
Quando as empresas falam em desperdícios, elas geralmente falam sobre os três tipos de desperdício: Muda, Mura e Muri. No entanto, muitas pessoas que tiveram contato com o Lean Manufacturing apenas têm o conhecimento dos oito desperdícios e do Muda, pois muitas delas ainda não foram apresentadas a Muri e Mura.
No entanto, esses desperdícios geralmente são muito mais importantes do que o Muda, e muitas vezes esses desperdícios podem ser as causas que provocam quando se olha o processo de uma maneira mais detalhada.
Muda por si só é a ação que não agrega valor nenhum a um processo; Mura é uma desigualdade no fluxo ou variação imprevisível no processo; já Muri é sobrecarregar recursos além da capacidade do seu processo na empresa. Abaixo, eu vou falar um pouco mais sobre isso:
Muda e os Oito Desperdícios
Como já foi falado, Muda é basicamente qualquer atividade ou processo que não agrega valor nenhum; podendo ser um desperdício físico de seu tempo, seus recursos e, finalmente, seu dinheiro.
Esses desperdícios foram categorizados por Taiichi Ohno dentro do sistema de produção da Toyota; sendo eles:
- Defeitos que ocorrem quando o produto não está apto para o uso. Isso resulta em perca de tempo, desmantelamento de produtos, retrabalho, e ainda pode provocar insatisfação do cliente;
- Excesso de processamento que pode ser causado por falhas do processo ou por itens que não agregam valor ao processo;
- Superprodução que gera um grande estoque desnecessário;
- Tempo de espera entre as etapas do processo;
- Inventário com excedente de peças (ou produtos);
- Transporte de materiais de um lugar para o outro;
- Movimentação desnecessária de homens ou de máquina;
- Não utilizar os talentos (ou habilidades) dos funcionários;
- Desperdício de recurso quando não se desliga luzes e máquinas quando não estão sendo utilizadas;
- Desperdício de subprodutos que não estão sendo usados no processo.
Mura – Desigualdade no Fluxo
Mura é o desperdício da desigualdade que praticamente provoca Muda, pois ao não atenuarmos a nossa demanda, colocamos demandas desiguais em nossos processos e pessoas, causando a criação de inventário e outros desperdícios citados acima.
Um exemplo bem óbvio disso são os processos de produção em que um gerente é medido na sua produção mensal. Nesses tipos de processos, os departamentos geralmente “correm que nem loucos” na última semana do mês para cumprir as metas, usando componentes e produzindo peças que não são realmente necessárias.
Nesse relato já conseguimos ver sinais de desperdício, sendo que na primeira semana do mês seguinte ocorre geralmente a escassez de componentes e o descumprimento das metas, pois o ideal é para evitar desperdício, suavizar a produção e trabalhar com a demanda do cliente, para não gerar estoque desnecessário e nem enlouquecer os operadores com uma demanda muito abusiva, pois isso pode provocar um aumento de falhas no processo.
Muri - Desperdício da Sobrecarga
Aproveitando o exemplo acima, o Muri é basicamente o estresse desnecessário que os operadores do processo acima estão passando. O Muri é causado pelo Mura e por uma série de outras falhas em nosso sistema, como falta de treinamento, formas de trabalho não muito claras ou inexistentes, ferramentas erradas e medidas mal pensadas de desempenho.
Analisando os três tipos de desperdício podemos ver que o Mura causa Muda, e que os oito desperdícios são sintomas de nossa falha em enfrentar Mura e Muri dentro de nossos processos, não a causa raiz!
Removendo os desperdícios de Muda, Mura e Muri
Primeiramente, você deve se concentrar em garantir que seu Mura seja removido, criando um fluxo previsível em nível; isso por sua vez, destaca o Muri (sobrecarga do processo) dentro do seu sistema, que pode ser eliminado. Ao seguir essa linha de raciocínio, você conseguirá eliminar grande parte do Muda presente em seu sistema.
Muda, Mura e Muri podem ser eliminados ou significativamente reduzidos se você implementar as várias ferramentas e princípios Lean. Mas não se apresse ao tentar se destacar fazendo mudanças rápidas para remover esses desperdícios e causar uma rápida impressão em seu chefe, pois isso pode ser um sucesso de curta duração ;)
Obs: Sempre se planeje muito bem para enfrentar Muda, Mura, e Muri, para que outros desperdícios de Muda não voltem para assombrá-lo.
Frases de Taiichi Ohno
Visando complementar um pouco essa postagem, eu elaborei um vídeo bem simples com 10 frases de Taiichi Ohno, que como nós vimos acima, foi ele quem estabeleceu as bases dessa filosofia maravilhosa que é o Lean Manufacturing, logo seria bem interessante vocês darem uma olhada no link do vídeo abaixo ;)
Conclusão e Recomendações
O artigo é apenas um resumo dessa metodologia maravilhosa para a redução de desperdícios que é o Lean Manufacturing, que nos ajuda muito de maneira bem organizada a fazer projetos de melhoria continua, como você já deve ter visto acima.
Eu sou um Green Belt recém-formado e caso você queira saber mais sobre essa metodologia maravilhosa, ou até fazer um curso sobre ela: eu recomendo os cursos de Green Belt e Black Belt do meu amigo Thiago Cardoso, que é Lean Six Sigma Master Black Belt e Scrum Master, que já fez vários projetos aplicando os conceitos de melhoria contínua; o cara é um expert no assunto.
Como você deve ter ficado na curiosidade de conhecer o mundo Belt dos projetos de melhoria contínua, abaixo tem um link de um vídeo do Thiago Cardoso falando de uma maneira bem mais detalhada sobre os oito desperdícios e como tornar o ambiente de trabalho mais produtivo.
Referências
- https://www.goskills.com/Lean-Six-Sigma (acessado em 09/12/2019 às 20:19)
- https://goleansixsigma.com/what-is-lean-six-sigma/ (acessado em 09/12/2019 às 20:28)
- Notas de aulas de Lean Six Sigma, Thiago Cardoso, Brains Desenvolvimento Profissional, 2019.
- https://www.manufacturing.net/home/article/13193437/the-principles-of-lean-manufacturing (acessado em 27/12/2019 às 20:28)
- https://leanmanufacturingtools.org/71/muda-mura-and-muri-lean-manufacturing-wastes/ (acessado em 29/12/2019 às 20:11)
- http://www.leansixsigmadefinition.com/glossary/5s/ (acessado em 29/12/2019 às 20:15)
- https://www.lucidchart.com/blog/plan-do-check-act-cycle (acessado em 01/01/2020 às 13:13)
- https://www.shmula.com/about-peter-abilla/what-is-mura-muri-muda/ (acessado em 01/01/2020 às 13:39)
Sobre o autor
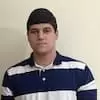
2 Comentários de "Lean Manufacturing (Manufatura Enxuta) e a redução de desperdícios na Indústria"
O que é o lean startup e como funciona essa metodologia?
Olá anônimo
O Lean Startup é uma metodologia de desenvolvimento de negócios e produtos com foco em velocidade, aprendizado e adaptabilidade.
A abordagem Científica do Lean Startup fornece uma abordagem científica para criar e gerenciar startups. Ela Trata de testar hipóteses, medir o progresso e aprender com os clientes. Em vez de construir cegamente um produto, enfatiza a experimentação contínua.
Comece com uma pergunta: em vez de perguntar: “Este produto pode ser construído?” a Lean Startup pergunta: “Este produto deve ser construído?” e “Podemos construir um negócio sustentável em torno disso?” Ele trata cada startup como um grande experimento.
Produto Mínimo Viável (PMV): Comece criando uma versão básica do seu produto (o PMV). Isso permite que você obtenha feedback de usuários reais desde o início. Se for bem sucedido, fornece uma base para um maior desenvolvimento.
Construir-Medir-Aprender: A startup enxuta segue um ciclo de feedback:
Construir: Crie o PMV.
Medir: Colete dados sobre como os usuários interagem com ele.
Aprenda: use insights para melhorar ou dinamizar.
Aprendizagem Validada: O objetivo é validar suposições sobre o seu produto. Se suas suposições estiverem erradas, você gira (muda de direção). Se eles estiverem certos, você persevera.
Lançamentos iterativos: em vez de esperar meses ou anos, libere seu produto de forma incremental. Aprenda com cada versão e ajuste de acordo.
Desenvolvimento do cliente: envolva-se com clientes em potencial desde o início. Não construa isoladamente. Entenda suas necessidades e pontos problemáticos.
Falhar Rápido, Falhar Barato: Aceite o fracasso como parte do processo. Fracasse rapidamente e aprenda com isso sem desperdiçar recursos.
Inovação Contínua: Continue refinando seu produto com base em feedback do mundo real. Adapte-se conforme você avança.
Ordem, não caos: Lean não significa apenas gastar menos dinheiro; trata-se de colocar uma metodologia em torno do desenvolvimento de produtos. Ele fornece ferramentas para eliminar incertezas e trabalhar de maneira mais inteligente.
Lembre-se de que a Lean Startup não é uma solução única para todos, mas oferece princípios valiosos para navegar no mundo imprevisível das startups.
Espero ter ajudado
Um abraço
Os comentários são sempre bem vindos, pois agregam valor ao artigo. Porém, existem algumas regras na Política de Comentários, que devem ser seguidas para o seu comentário não ser excluído:
- Os comentários devem estar relacionados ao assunto do artigo.
- Jamais faça um comentário com linguagem ofensiva ou de baixo calão, que deprecie o artigo exposto ou que ofenda o autor ou algum leitor do blog.
- Não coloque links de sites ou blogs no corpo do texto do comentário. Para isso, assine com seu Nome/URL ou OpenID.
-Não coloque seu email e nem seu telefone no corpo do texto do comentário. Use o nosso formulário de contato.
- Se encontrar algum pequeno erro na postagem, por favor, seja bem claro no comentário, pois a minha bola de cristal não é muito boa.
- Tem vezes que eu demoro pra responder, mas quase sempre eu respondo.
- Não seja tímido, se você tem alguma duvida ou sabe de algo mais sobre o assunto abordado no artigo, comente e compartilhe conosco :)